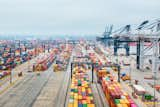
What Trump’s Tariffs Could Mean for Home Building—and the Housing Crisis
After President Trump announced his tariffs plan on April 2, what he has deemed "Liberation Day," only to follow up with a 90-day pause on the previously announced reciprocal tariffs (with exception to a 10 percent flat duty on all imported goods), the public is rightfully flummoxed about precisely what products are about to get more expensive. Homebuilders fall into this shaky boat: According to the National Association of Homebuilders (NAHB), nearly $14 billion of imported goods were used to construct new single- and multifamily residences across the country—accounting for seven percent of all required materials. Though there’s still much uncertainty about how tariffs will resume after the pause, reports nationwide have homebuilders of all sizes bracing for what could be a big setback to creating new homes and renovating others.
When it comes to home building, the industry isn’t a stranger to pricing changes to materials like softwood and steel, which were tariffed by Trump in his first term (and mostly maintained under the Biden administration). However, the U.S. Department of Commerce has stated that it plans to raise these tariffs again this year to more than 34 percent, which, says the Financial Times, includes new import and anti-dumping duties. It’s unknown when this plan will go into effect. And while Canada is also a major exporter of steel and aluminum, according to U.S. News & World Report, many of the materials used in U.S. housing construction come from China, currently subject to a whopping 145 percent tariff (which includes a 120 percent reciprocal tariff exempted from his April 9 pauses). This could cause material costs to soar to as much as $45 billion per year from today’s $4 billion expenditure.
Other materials, including gypsum for drywall, flooring, appliances, and HVAC systems are frequently made in and imported from Canada, China, and Mexico; in early April, the New York Times published example "line items" that account for both tariff costs and possible labor shortages resulting from large-scale migrant worker deportations. In their analysis, the costs for windows and doors would increase by 11 percent, roofing would increase by 21 percent, and drywall would increase by 22 percent—not including any cost increases to labor. U.S. News notes that suppliers and contractors may be able to source materials more cheaply by shopping from manufacturers in countries currently exempted from reciprocal tariffs, but "most homebuilders have developed relationships with companies and countries and can’t always make immediate changes."
Yet immediate changes are coming from the top—policy shifts at the national level cause prices to fluctuate, which, as a story by the Pittsburgh Gazette explains, has strained some smaller suppliers and contractors. One Pennsylvania supplier who typically receives prices annually has begun to see them change almost daily; some manufacturers have paused pricing entirely, which can delay projects. This could mean that projects currently underway could see price hikes or pauses while manufacturers catch up or developers strategize how to recoup potential unanticipated costs.
For smaller remodeling projects, the NAHB reports that their 2025 first quarter Remodeling Market Index—a survey that asks builders to rate the remodeling market—dropped to its lowest level since 2020, "as some remodelers are reporting that uncertainty about tariffs and the direction of the economy are making customers hesitant to spend on larger projects," says Nicole Goolsby, the remodelers chair for NAHB. Even larger homebuilders like Lennar were feeling "squeezed" as early as March and, according to Realtor.com, their market share dropped by four percent due to interest rates and a downturn in consumer confidence in the wake of international trade uncertainty.
This means consumers could see higher prices for new construction homes as well as for renovations to existing ones. Realtor.com notes that new homes account for less than 20 percent of the housing market, but that there are some states where construction is booming to meet demand: In Idaho, new construction makes up nearly 40 percent of the market, and in North Carolina and Delaware, new homes hover around 30 percent of the housing market. In these states, momentum toward meeting our current housing needs could be hit hard as the NAHB reports that a rise in material costs could raise new home construction costs by more than $9,000. As import duties are levied on individual materials themselves, the costs could be passed onto buyers, raising more questions about how trade policy will ultimately impact the housing crisis.
Top photo by Brandon Bell/Getty Images.
Related Reading:
Published
Topics
Design NewsGet the Pro Newsletter
What’s new in the design world? Stay up to date with our essential dispatches for design professionals.